How to Find the Best Packaging Machine Repair Company Near You
The Ultimate Guide to Packaging Device Repair Service: Maintain Your Procedures Running Efficiently
Comprehending the complexities of packaging equipment repair service is essential for maintaining optimum performance and minimizing disturbances. Routine maintenance not just extends the life of these equipments however also addresses usual problems that can impede performance.
Significance of Normal Maintenance
Normal maintenance of product packaging makers is essential for making certain ideal efficiency and durability. By implementing an organized upkeep routine, drivers can determine possible issues prior to they escalate right into significant issues. This aggressive method not just minimizes downtime however also prolongs the life-span of the equipment, eventually leading to decreased functional costs.
Routine examinations enable the evaluation of critical elements such as belts, seals, and sensors. Addressing deterioration without delay prevents unforeseen failures that can interrupt manufacturing and cause expensive repair services. In addition, routine maintenance assists make certain conformity with industry standards and policies, promoting a secure workplace.
Moreover, maintenance activities such as cleansing, lubrication, and calibration dramatically improve equipment efficiency. Improved performance translates to consistent product quality, which is vital for maintaining customer complete satisfaction and brand credibility. A well-kept packaging device operates at optimal rates and lowers product waste, adding to general efficiency.
Typical Packaging Machine Concerns
Product packaging makers, like any type of complicated machinery, can encounter a selection of usual problems that may hinder their efficiency and effectiveness - packaging machine repair. One common problem is irregular securing, which can result in product perishing and wastefulness if bundles are not properly secured. This commonly results from misaligned components or used sealing elements
An additional regular issue is mechanical jams, which can take place because of foreign things, worn components, or incorrect alignment. Jams can create delays in manufacturing and boost downtime, ultimately influencing general performance. Furthermore, electronic breakdowns, such as failure in sensing units or control systems, can disrupt procedures and lead to incorrect dimensions or unpredictable equipment habits.
Furthermore, problems with item feed can likewise emerge, where items might not be delivered to the product packaging location constantly, creating disruptions. Last but not least, deterioration on rollers and belts can lead to suboptimal efficiency, calling for immediate focus to prevent additional damages.
Recognizing these common issues is crucial for maintaining the stability of product packaging procedures, ensuring that machinery runs efficiently and successfully, which in turn helps in meeting manufacturing targets and keeping item quality.
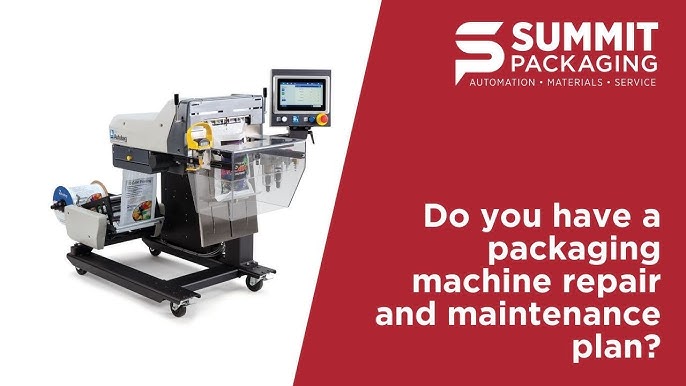
Troubleshooting Strategies
Efficient troubleshooting strategies are necessary for immediately dealing with concerns that develop with packaging equipments. A methodical approach is important for determining the source of malfunctions and lessening downtime. Begin by gathering details about the signs and symptoms observed; this might consist of unusual noises, operational hold-ups, or mistake codes presented on the machine's user interface.
Next, refer to the equipment's guidebook for fixing standards specific to the version concerned. This resource can provide beneficial understandings into common concerns and advised analysis steps. Utilize aesthetic examinations to look for loosened connections, used belts, or misaligned elements, as these physical variables typically add to operational failings.
Apply a process of elimination by screening specific device features. If a seal is not developing appropriately, assess the sealing system and temperature setups to establish if they fulfill operational specifications. File each step taken and the outcomes observed, as this can help in future repairing initiatives.
Repair vs. Replacement Decisions
When confronted with equipment malfunctions, deciding whether to change a product packaging or repair device can be a complex and crucial choice. This decision rests on numerous crucial aspects, including the age of the machine, the extent of the damages, and the forecasted effect on operational efficiency.
To start with, take into consideration the maker's age. Older devices may call for more frequent repairs, bring about greater cumulative prices that can go beyond the investment in a new device. Furthermore, evaluate the extent of the breakdown. Minor concerns can typically be fixed quickly and cost effectively, whereas comprehensive damages may necessitate a significant monetary commitment for repair services.
Operational downtime is an additional important factor to consider. If repairing the equipment will create prolonged delays, purchasing a site new maker that offers improved performance and dependability may be more prudent. Take into consideration the schedule of parts; if replacement components are difficult to come by, it may be a lot more critical to change the machine entirely.
Ultimately, carrying out a cost-benefit analysis that consists of both instant and lasting effects will certainly assist in making an educated choice that straightens with your functional objectives and financial restraints. (packaging machine repair)
Preventative Actions for Long Life
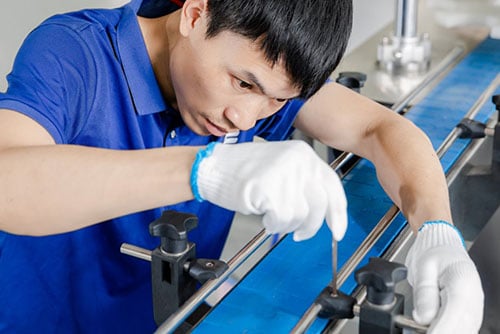
Key safety nets consist of regular lubrication of moving parts, positioning checks, and calibration of controls and sensing units. Developing a cleansing schedule to remove debris and pollutants from equipment can substantially lower wear and tear (packaging machine repair). Additionally, keeping track of operational specifications such as temperature level and resonance can assist find abnormalities beforehand
Educating team to identify indicators of wear or breakdown is an additional crucial component of preventive upkeep. Encouraging drivers with the expertise to execute standard troubleshooting can bring about quicker resolutions and decrease functional disruptions.
Paperwork of maintenance activities, including service documents and examination searchings for, promotes responsibility and helps with informed decision-making regarding repairs and substitutes. By prioritizing safety nets, services can ensure their packaging equipments run at peak performance, ultimately bring about boosted blog efficiency and reduced functional expenses.
Conclusion
In conclusion, the efficient upkeep and fixing of packaging devices are extremely important for sustaining operational effectiveness. By applying preventive steps, services can boost machine longevity and make sure nonstop performance in packaging operations.
Understanding the ins and outs of product packaging equipment fixing is crucial for preserving ideal performance and lessening disturbances.Normal upkeep of product packaging equipments is crucial for ensuring optimal performance and longevity.Packaging machines, like any type of complicated equipment, can encounter a variety of usual concerns that might prevent their efficiency and effectiveness. If fixing the maker will cause prolonged delays, spending in a brand-new maker that uses improved effectiveness and reliability might be extra sensible.In final thought, the efficient maintenance and repair of product packaging makers are vital for sustaining operational performance.